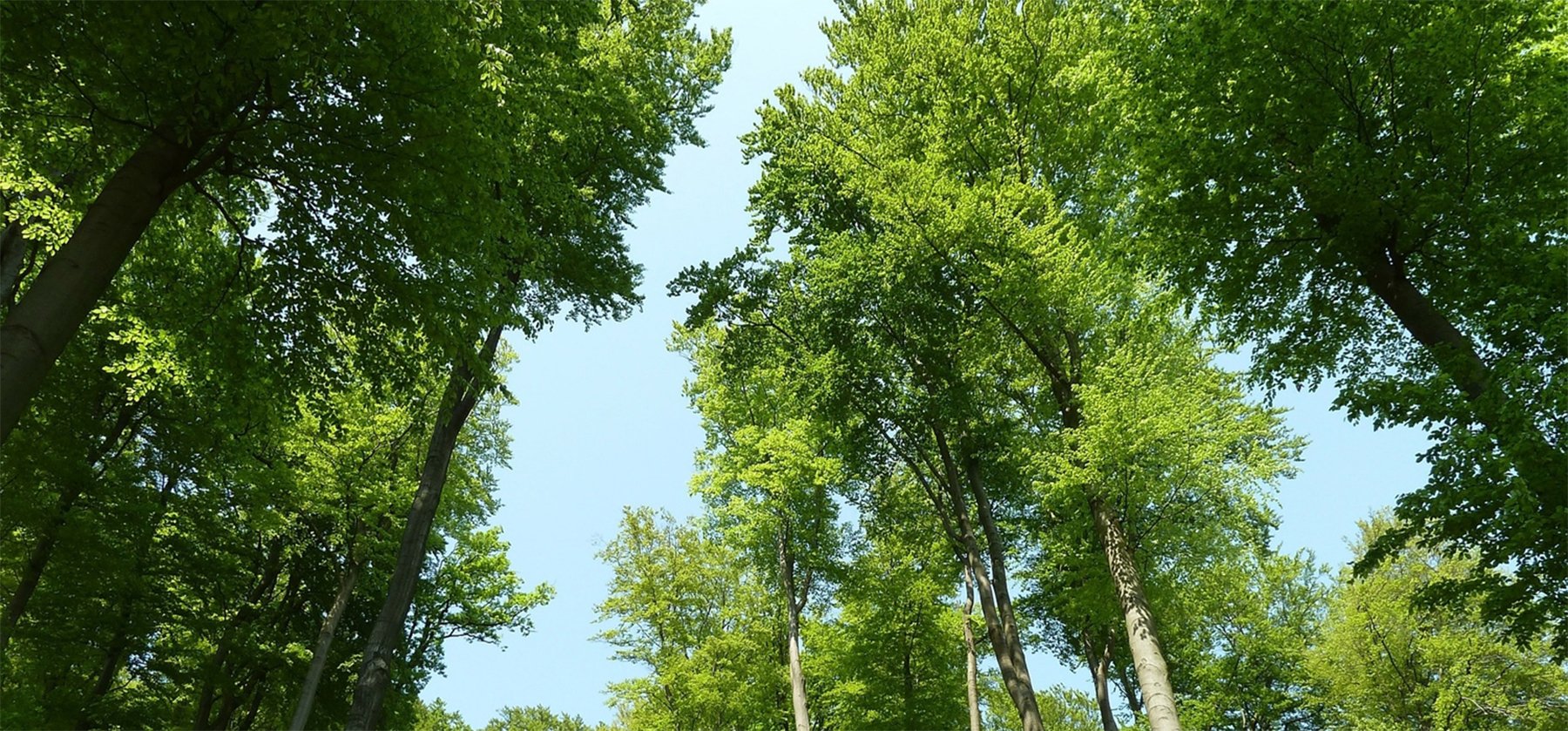
„From a tree to a chair”
Wood, like no other natural product, has been associated with humans for millennia to the present day.
Common Beech (Fagus sylvatica) – is a species of deciduous tree that is found in large numbers in Europe and Poland. The beech grows slowly, reaching a maximum height of even forty meters, with a trunk diameter of up to 1.5 meters. Beech wood is characterized by high hardness, durability and strength, it is susceptible to gluing, grinding, dyeing, varnishing and as one the few is plastic; therefore, it is ideal for bending. All these advantages decided that as much as 90% of our production is made of beech wood. Other species of trees that we use for the production of furniture are: oak, acacia, ash, walnut.